Vacuum packaging is essential in the meat industry to extend shelf life, preserve freshness, and prevent contamination. However, the performance of meat vacuum packaging depends heavily on the durability of the flexible barrier materials used. Over time, mechanical stress such as twisting, folding, and crushing during handling and distribution can lead to pinhole formation, jeopardizing product safety. This is where flex durability testing, particularly the Gelbo flex test method, becomes critical. This article offers a professional guide to evaluating meat vacuum packaging materials using ASTM F392, helping packaging engineers and QC professionals make informed decisions.
The Importance of Flex Testing for Meat Vacuum Packaging
Flexible barrier films used in meat vacuum packaging must withstand mechanical stresses without compromising their barrier properties. Failures like pinholes or ply separation can lead to oxygen ingress and moisture transfer, which accelerates spoilage and reduces product quality. ASTM F392 provides a standardized conditioning method to simulate these flexing conditions in a controlled laboratory setting.
By replicating real-world transportation and handling scenarios, flex testing helps identify weak points in packaging materials before they reach the market, reducing product recalls and improving brand reputation.
Flex Tester and Gelbo Flex Test Method in ASTM F392
ASTM F392 utilizes a Gelbo flex test method, which involves twisting and crushing motions to simulate repeated mechanical stress on packaging films. The flex tester is specially designed to apply controlled stress through cyclic motion at a rate of 45 cycles per minute. This section explains the key elements of the method:
Flex Tester Design
ది Cell Instruments ఫ్లెక్స్ డ్యూరబిలిటీ టెస్టర్, compliant with ASTM F392, features:
- Two mandrels spaced 180 mm apart at start position.
- A twisting motion of 440° followed by a horizontal displacement of 65 mm.
- Testing capability for both full flex and partial flex cycles.
This design replicates the combined stress effects that packaging films face during storage and logistics.
Test Conditions and Cycles
ASTM F392 defines five standard flex conditioning levels:
Condition | Cycles | Duration at 45 cpm | Purpose |
---|---|---|---|
A | 2700 | 1 hour | Severe stress simulation |
B | 900 | 20 minutes | Moderate stress |
C | 270 | 6 minutes | Light stress |
D | 20 | Partial damage detection | |
E | 20 (Partial flex only) | Short stroke, mild twist | Minimal stress detection |
For meat vacuum packaging, Condition A or B is often selected to simulate intense shipping and handling environments, where long-distance cold-chain logistics is common.
Preparing meat vacuum packaging Specimens for Flex Testing
To ensure accurate results:
- Cut samples into 200 mm × 280 mm sheets.
- Use double-sided tape to fix the film edges to the tester’s mandrels.
- Avoid sealing the short edges to allow natural material deformation.
- Condition samples for 24 hours at 23 ± 2°C and 50 ± 5% RH before testing.
Post-testing evaluations may include barrier property assessments like oxygen transmission rate (OTR) or visual pinhole detection.
Barrier Integrity Post Flex Evaluating for meat vacuum packaging
After flexing, packaging materials are assessed for:
- Pinhole formation: using dye penetration, vacuum decay, or bubble leak detection methods.
- Loss of barrier properties: via gas or moisture permeability testing.
If pinholes exceed acceptable limits or barrier performance drops significantly, the packaging structure or material formulation may require redesign.
Why Use Cell Instruments Flex Durability Tester?
For accurate and repeatable results, it’s crucial to use a reliable and compliant testing system. Cell Instruments’ ఫ్లెక్స్ డ్యూరబిలిటీ టెస్టర్ offers:
- Full compliance with ASTM F392 specifications.
- Adjustable flexing conditions to simulate different distribution environments.
- High durability and repeatability, suitable for daily QC operations and R&D labs.
Integrating our solution into your packaging validation process ensures meat vacuum packaging materials meet performance expectations and regulatory requirements.
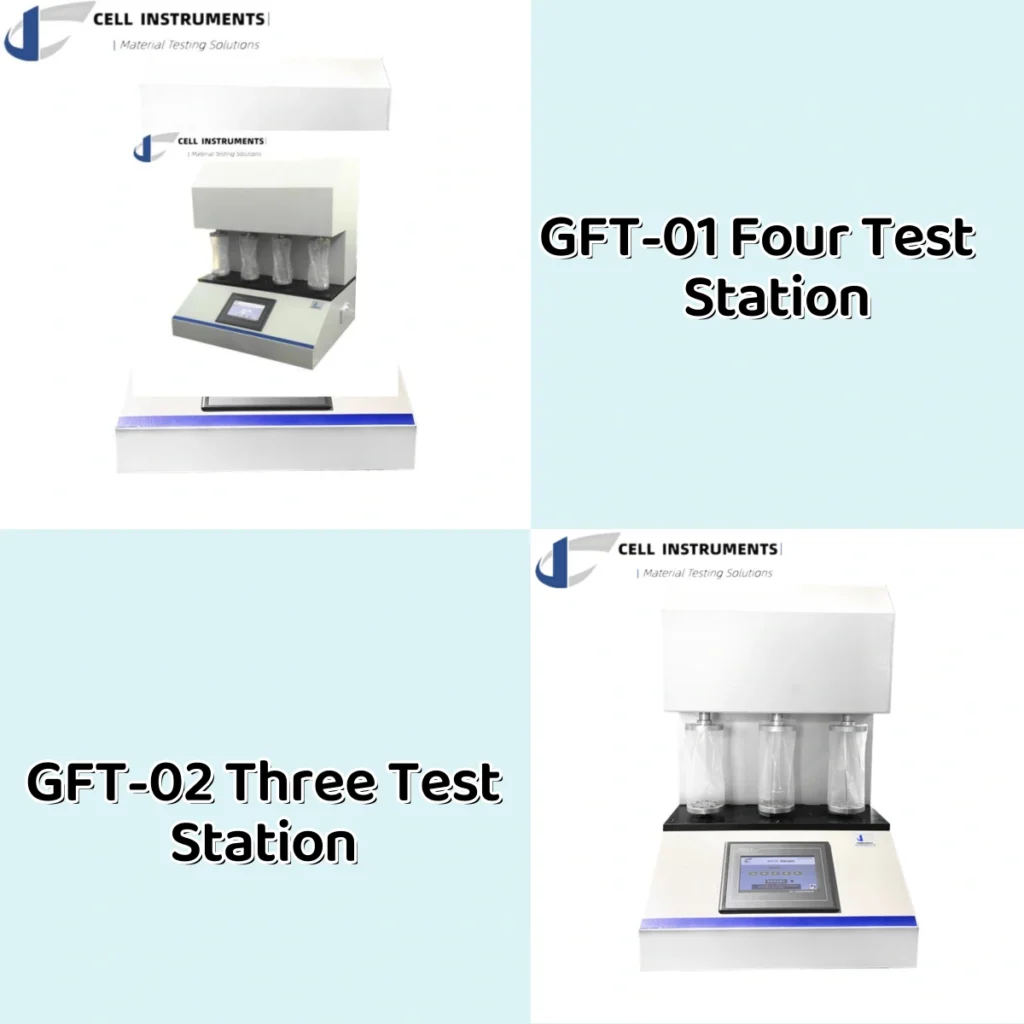
Conclusion
Effective meat vacuum packaging is not just about barrier performance under static conditions—durability under mechanical stress is equally important. By applying the Gelbo flex test method outlined in ASTM F392, professionals can assess and improve the reliability of packaging films used in meat products. Selecting the right flex tester, such as the one provided by Cell Instruments, ensures standard-compliant, efficient, and insightful test results.
FAQ
- Why is flex durability important for meat vacuum packaging?
It prevents barrier failure during transport and handling, ensuring product freshness and safety. - What does the Gelbo flex test simulate?
It replicates twisting and crushing stress to mimic mechanical damage during logistics. - Which ASTM standard covers flex testing for packaging films?
ASTM F392 outlines the procedure for conditioning flexible barrier materials for flex durability. - How can I detect pinholes after flex testing?
Through visual inspection, dye penetration, or barrier property testing such as OTR. - What equipment is suitable for ASTM F392 testing?
Cell Instruments’ Flex Durability Tester meets all technical specifications required by ASTM F392.